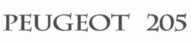
Peugeot 205 Manual
Main and big-end bearings - inspectionEngine removal and overhaul procedures / Main and big-end bearings - inspection
Inspection
1 Even though the main and big-end bearing
shells should be renewed during the engine
overhaul, the old shells should be retained for
close examination, as they may reveal
valuable information about the condition of
the engine.
2 Bearing failure occurs because of lack of lubrication, the presence of dirt or other foreign particles, overloading the engine, and corrosion (see illustration).
10.2 Typical bearing failures
A Scratched by dirt; dirt embedded in bearing material
B Lack of oil; overlay wiped out
C Improper seating; bright (polished sections)
D Tapered journal; overlay gone from entire surface
E Radius ride
F Fatigue failure; craters or pockets
Regardless of the cause of bearing failure, the cause must be corrected (where applicable) before the engine is reassembled, to prevent it from happening again.
3 When examining the bearing shells, remove them from the cylinder block/crankcase and main bearing caps, and from the connecting rods and the big-end bearing caps, then lay them out on a clean surface in the same general position as their location in the engine. This will enable you to match any bearing problems with the corresponding crankshaft journal. Do not touch any shell’s bearing surface with your fingers while checking it, or the delicate surface may be scratched.
4 Dirt or other foreign matter gets into the engine in a variety of ways. It may be left in the engine during assembly, or it may pass through filters or the crankcase ventilation system. It may get into the oil, and from there into the bearings. Metal chips from machining operations and normal engine wear are often present. Abrasives are sometimes left in engine components after reconditioning, especially when parts are not thoroughly cleaned using the proper cleaning methods.
Whatever the source, these foreign objects often end up embedded in the soft bearing material, and are easily recognised. Large particles will not embed in the material, and will score or gouge the shell and journal. The best prevention for this cause of bearing failure is to clean all parts thoroughly, and to keep everything spotlessly-clean during engine assembly. Frequent and regular engine oil and filter changes are also recommended.
5 Lack of lubrication (or lubrication breakdown) has a number of inter-related causes. Excessive heat (which thins the oil), overloading (which squeezes the oil from the bearing face) and oil leakage (from excessive bearing clearances, worn oil pump or high engine speeds) all contribute to lubrication breakdown. Blocked oil passages, which usually are the result of misaligned oil holes in a bearing shell, will also starve a bearing of oil, and destroy it. When lack of lubrication is the cause of bearing failure, the bearing material is wiped or extruded from the shell’s steel backing. Temperatures may increase to the point where the steel backing turns blue from overheating.
6 Driving habits can have a definite effect on bearing life. Full-throttle, low-speed operation (labouring the engine) puts very high loads on bearings, which tends to squeeze out the oil film. These loads cause the shells to flex, which produces fine cracks in the bearing face (fatigue failure). Eventually, the bearing material will loosen in pieces, and tear away from the steel backing.
7 Short-distance driving leads to corrosion of bearings, because insufficient engine heat is produced to drive off condensed water and corrosive gases. These products collect in the engine oil, forming acid and sludge. As the oil is carried to the engine bearings, the acid attacks and corrodes the bearing material.
8 Incorrect shell refitting during engine assembly will lead to bearing failure as well.
Tight-fitting shells leave insufficient bearing running clearance, and will result in oil starvation. Dirt or foreign particles trapped behind a bearing shell result in high spots on the bearing, which lead to failure.
9 Do not touch any shell’s bearing surface with your fingers during reassembly; there is a risk of scratching the delicate surface, or of depositing particles of dirt on it.




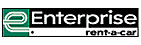
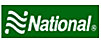

