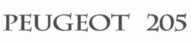
Peugeot 205 Manual
Cylinder head - removal and refittingTU series engine in-car repair procedures / Cylinder head - removal and refitting
Removal
1 Disconnect the battery negative lead.
2 Drain the cooling system as described in Chapter 1.
3 Remove the cylinder head cover as described in Section 4.
4 Align the engine assembly/valve timing holes as described in Section 3, and lock both the camshaft sprocket and flywheel in position. Do not attempt to rotate the engine whilst the tools are in position.
5 Note that the following text assumes that the cylinder head will be removed with both inlet and exhaust manifolds attached; this is easier, but makes it a bulky and heavy assembly to handle. If it is wished to remove the manifolds first, proceed as described in the relevant Part of Chapter 4.
6 Working as described in the relevant Part of Chapter 4, disconnect the exhaust system front pipe from the manifold. Where fitted, disconnect or release the oxygen sensor wiring, so that it is not strained by the weight of the exhaust.
7 Remove the air cleaner assembly and inlet ducts as described in Chapter 4.
8 On carburettor engines, disconnect the following from the carburettor and inlet manifold as described in Chapter 4A: a) Fuel feed and return hoses (plug all openings, to prevent loss of fuel and the entry of dirt into the system).
b) Throttle cable.
c) Choke cable (where applicable).
d) Carburettor idle fuel cut-off solenoid wiring connector(s).
e) Vacuum servo unit vacuum hose, coolant hose and all other relevant breather/vacuum hoses from the manifold.
9 On fuel-injected engines, carry out the
following operations as described in Chapter
4B:
a) Depressurise the fuel system, and
disconnect the fuel feed and return hoses
from the throttle body (plug all openings,
to prevent loss of fuel and entry of dirt
into the fuel system).
b) Disconnect the throttle cable.
c) Disconnect the relevant electrical connectors from the throttle body.
d) Disconnect the vacuum servo unit hose, coolant hose(s) and all the other relevant/breather hoses from the manifold.
10 Remove the centre and upper timing belt covers as described in Section 6.
11 Loosen the timing belt tensioner pulley retaining nut. Pivot the pulley in a clockwise direction, using a suitable square-section key fitted to the hole in the pulley hub, then retighten the retaining nut.
12 Disengage the timing belt from the camshaft sprocket, and position the belt clear of the sprocket. Ensure that the belt is not bent or twisted sharply.
13 Slacken the retaining clips, and disconnect the coolant hoses from the thermostat housing (on the left-hand end of the cylinder head).
14 Depress the retaining clip(s), and disconnect the wiring connector(s) from the electrical switch and/or sensor(s) which are screwed into the thermostat housing/cylinder head (as appropriate). Also where necessary release the TDC sensor connector from its support on the distributor bracket on the lefthand end of the cylinder head.
Carburettor models
15 Disconnect the LT wiring connectors from
the distributor and HT coil. Release the TDC
sensor wiring connector from the side of the
coil mounting bracket, and disconnect the
vacuum pipe from the distributor vacuum
diaphragm unit. If the cylinder head is to be
dismantled for overhaul, remove the
distributor and ignition HT coil as described in
Chapter 5B. If the cylinder numbers are not
already marked on the HT leads, number each
lead, to avoid the possibility of the leads being
incorrectly connected on refitting. Disconnect
the HT leads from the spark plugs, and
remove the distributor cap and lead
assembly.
Fuel-injected models
16 Disconnect the wiring connector from the
ignition module. If the cylinder head is to be
dismantled for overhaul, remove the ignition
module as described in Chapter 5B. If the
cylinder numbers are not already marked on
the HT leads, number each lead, to avoid the
possibility of the leads being incorrectly
connected on refitting. Note that the HT leads
should be disconnected from the spark plugs
instead of the coil, and the coil and leads
removed as an assembly.
All models
17 Slacken and remove the bolt securing the
engine oil dipstick tube to the cylinder head.
18 Working in the reverse of the sequence shown in illustration 11.38, progressively slacken the ten cylinder head bolts by half a turn at a time, until all bolts can be unscrewed by hand.
19 With all the cylinder head bolts removed, lift the rocker arm assembly off the cylinder head. Note the locating pins which are fitted to the base of each rocker arm pedestal. If any pin is a loose fit in the head or pedestal, remove it for safe-keeping.
20 On engines with a cast-iron cylinder block, lift the cylinder head away; seek assistance if possible, as it is a heavy assembly, especially if it is being removed complete with the manifolds.
21 On engines with an aluminium cylinder block, the joint between the cylinder head and gasket and the cylinder block/crankcase must now be broken without disturbing the wet liners. To break the joint, obtain two L-shaped metal bars which fit into the cylinder head bolt holes. Gently “rock” the cylinder head free towards the front of the car (see illustration).
11.21 Using two angled metal rods to free the cylinder head from the block
Do not try to swivel the head on the cylinder block/crankcase; it is located by dowels, as well as by the tops of the liners. Note: If care is not taken and the liners are moved, there is also a possibility of the bottom seals being disturbed, causing leakage after refitting the head. When the joint is broken, lift the cylinder head away; seek assistance if possible, as it is a heavy assembly, especially if it is being removed complete with the manifolds.
22 On all models, remove the gasket from the top of the block, noting the two locating dowels. If the locating dowels are a loose fit, remove them and store them with the head for safe-keeping. Do not discard the gasket - on some models it will be needed for identification purposes (see paragraphs 28 and 29).
Caution: On aluminium block engines, Do not attempt to rotate the crankshaft with the cylinder head removed, otherwise the wet liners may be displaced. Operations that require the rotation of the crankshaft (eg cleaning the piston crowns), should only be carried out once the cylinder liners are firmly clamped in position. In the absence of the special Peugeot liner clamps, the liners can be clamped in position using large flat washers positioned underneath suitable-length bolts. Alternatively, the original head bolts could be temporarily refitted, with suitable spacers fitted to their shanks.
23 If the cylinder head is to be dismantled for overhaul, remove the camshaft as described in Section 10, then refer to Part D of this Chapter.
Preparation for refitting 24 The mating faces of the cylinder head and cylinder block/crankcase must be perfectly clean before refitting the head. Use a hard plastic or wood scraper to remove all traces of gasket and carbon; also clean the piston crowns. Refer to paragraph 23 before turning the crankshaft on aluminium block engines.
Take particular care during the cleaning operations, as aluminium alloy is easily damaged. Also, make sure that the carbon is not allowed to enter the oil and water passages - this is particularly important for the lubrication system, as carbon could block the oil supply to the engine’s components. Using adhesive tape and paper, seal the water, oil and bolt holes in the cylinder block/crankcase. To prevent carbon entering the gap between the pistons and bores, smear a little grease in the gap. After cleaning each piston, use a small brush to remove all traces of grease and carbon from the gap, then wipe away the remainder with a clean rag. Clean all the pistons in the same way.
25 Check the mating surfaces of the cylinder block/crankcase and the cylinder head for nicks, deep scratches and other damage. If slight, they may be removed carefully with a file, but if excessive, machining may be the only alternative to renewal.
26 If warpage of the cylinder head gasket surface is suspected, use a straight-edge to check it for distortion. Refer to Part D of this Chapter if necessary.
27 When purchasing a new cylinder head gasket, it is essential that a gasket of the correct thickness is obtained. On some models only one thickness of gasket is available, so this is not a problem. However on other models, there are two different thicknesses available - the standard gasket which is fitted at the factory, and a slightly thicker “repair” gasket (+ 0.2 mm), for use once the head gasket face has been machined. If the cylinder head has been machined, it should have the letter “R” stamped adjacent to the No 3 exhaust port, and the gasket should also have the letter “R” stamped adjacent to No 3 cylinder on its front upper face. The gaskets can also be identified as described in the following paragraph, using the cut-outs on the left-hand end of the gasket.
28 With the gasket fitted the correct way up on the cylinder block, there will be a single cut-out, or no cut-out at all, at the rear of the left-hand side of the gasket identifying the engine type (ie. TU engine). In the centre of the gasket there may be another series of between 0 and 4 cut-outs, identifying the manufacturer of the gasket and whether or not it contains asbestos (these cut-outs are of little importance). The important cut-out location is at the front of the gasket; on the standard gasket there will be no cut-out in this position, whereas on the thicker “repair” gasket there will be a single cut-out (see illustration).
11.28 Cylinder head gasket markings
A Engine type identification cut-outs B Gasket manufacturer identification cutouts C Gasket thickness identification cut-out
Identify the gasket type, and ensure that the new gasket obtained is of the correct thickness. If there is any doubt as to which gasket is fitted, take the old gasket along to your Peugeot dealer, and have him confirm the gasket type.
29 Check the condition of the cylinder head bolts, and particularly their threads, whenever they are removed. Wash the bolts in suitable solvent, and wipe them dry. Check each for any sign of visible wear or damage, renewing any bolt if necessary. Measure the length of each bolt, to check for stretching (although this is not a conclusive test, in the event that all ten bolts have stretched by the same amount). Although Peugeot do not actually specify that the bolts must be renewed, it is strongly recommended that the bolts should be renewed as a complete set whenever they are disturbed.
30 On aluminium block engines, prior to refitting the cylinder head, check the cylinder liner protrusion as described in Part D of this Chapter.
Refitting
31 Wipe clean the mating surfaces of the
cylinder head and cylinder block/crankcase.
Check that the two locating dowels are in position at each end of the cylinder block/crankcase surface and, if necessary, remove the cylinder liner clamps.
32 Position a new gasket on the cylinder block/crankcase surface, ensuring that its identification cut-outs are at the left-hand end of the gasket.
33 Check that the flywheel and camshaft sprocket are still correctly locked in position with their respective tools then, with the aid of an assistant, carefully refit the cylinder head assembly to the block, aligning it with the locating dowels.
34 Ensure that the locating pins are in position in the base of each rocker pedestal, then refit the rocker arm assembly to the cylinder head.
35 Apply a smear of grease to the threads, and to the underside of the heads, of the cylinder head bolts. Peugeot recommend the use of Molykote G Rapid Plus grease (available from your Peugeot dealer - a sachet is supplied with the top-end gasket set); in the absence of the specified grease, a goodquality high-melting-point grease may be used.
36 Carefully enter each bolt into its relevant hole (do not drop them in) and screw in, by hand only, until finger-tight.
37 Working progressively and in the sequence shown, tighten the cylinder head bolts to their Stage 1 torque setting, using a torque wrench and suitable socket (see illustrations).
11.37a Cylinder head bolt tightening sequence
11.37b Working in the sequence, tighten the head bolts first with a torque
wrench . . .
38 Once all the bolts have been tightened to their Stage 1 setting, working again in the given sequence, angle-tighten the bolts through the specified Stage 2 angle, using a socket and extension bar. It is recommended that an angle-measuring gauge is used during this stage of the tightening, to ensure accuracy (see illustration).
11.38 . . . then with an angle tightening gauge
If a gauge is not available, use white paint to make alignment marks between the bolt head and cylinder head prior to tightening; the marks can then be used to check that the bolt has been rotated through the correct angle during tightening.
39 On cast-iron block engines, it will then be necessary to tighten the bolts through the specified Stage 3 angle setting.
40 With the cylinder head bolts correctly tightened, refit the dipstick tube retaining bolt and tighten it securely.
41 Refit the timing belt to the camshaft sprocket. Ensure that the “front run” of the belt is taut - ie, ensure that any slack is on the tensioner pulley side of the belt. Do not twist the belt sharply while refitting it, and ensure that the belt teeth are seated centrally in the sprockets.
42 Loosen the tensioner pulley retaining nut.
Pivot the pulley anti-clockwise to remove all free play from the timing belt, then retighten the nut.
43 Tension the belt as described under the relevant sub-heading in Section 7, then refit the centre and upper timing belt covers as described in Section 6.
Carburettor models
44 If the head was stripped for overhaul, refit
the distributor and HT coil as described in
Chapter 5B, ensuring that the HT leads are
correctly reconnected. If the head was not
stripped, reconnect the wiring connector and
vacuum pipe to the distributor, and the HT
lead to the coil; clip the TDC sensor wiring
connector onto the coil bracket.
Fuel-injected models
45 If the head was stripped for overhaul, refit
the ignition module and leads as described in
Chapter 5B, ensuring that the leads are
correctly reconnected. If the head was not
stripped, simply reconnect the wiring
connector to the module.
All models
46 Reconnect the wiring connector(s) to the
coolant switch/sensor(s) on the left-hand end
of the head.
47 Reconnect the coolant hoses to the thermostat housing, securely tightening their retaining clips.
48 Working as described in the relevant Part of Chapter 4, carry out the following tasks: a) Refit all disturbed wiring, hoses and control cable(s) to the inlet manifold and fuel system components.
b) Reconnect and adjust the choke and throttle cables as applicable.
d) Reconnect the exhaust system front pipe to the manifold. Where applicable, reconnect the oxygen sensor wiring connector.
e) Refit the air cleaner assembly and ducting.
49 Check and, if necessary, adjust the valve clearances as described in Section 5.
50 On completion, reconnect the battery, and refill the cooling system as described in Chapter 1.




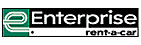
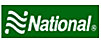

